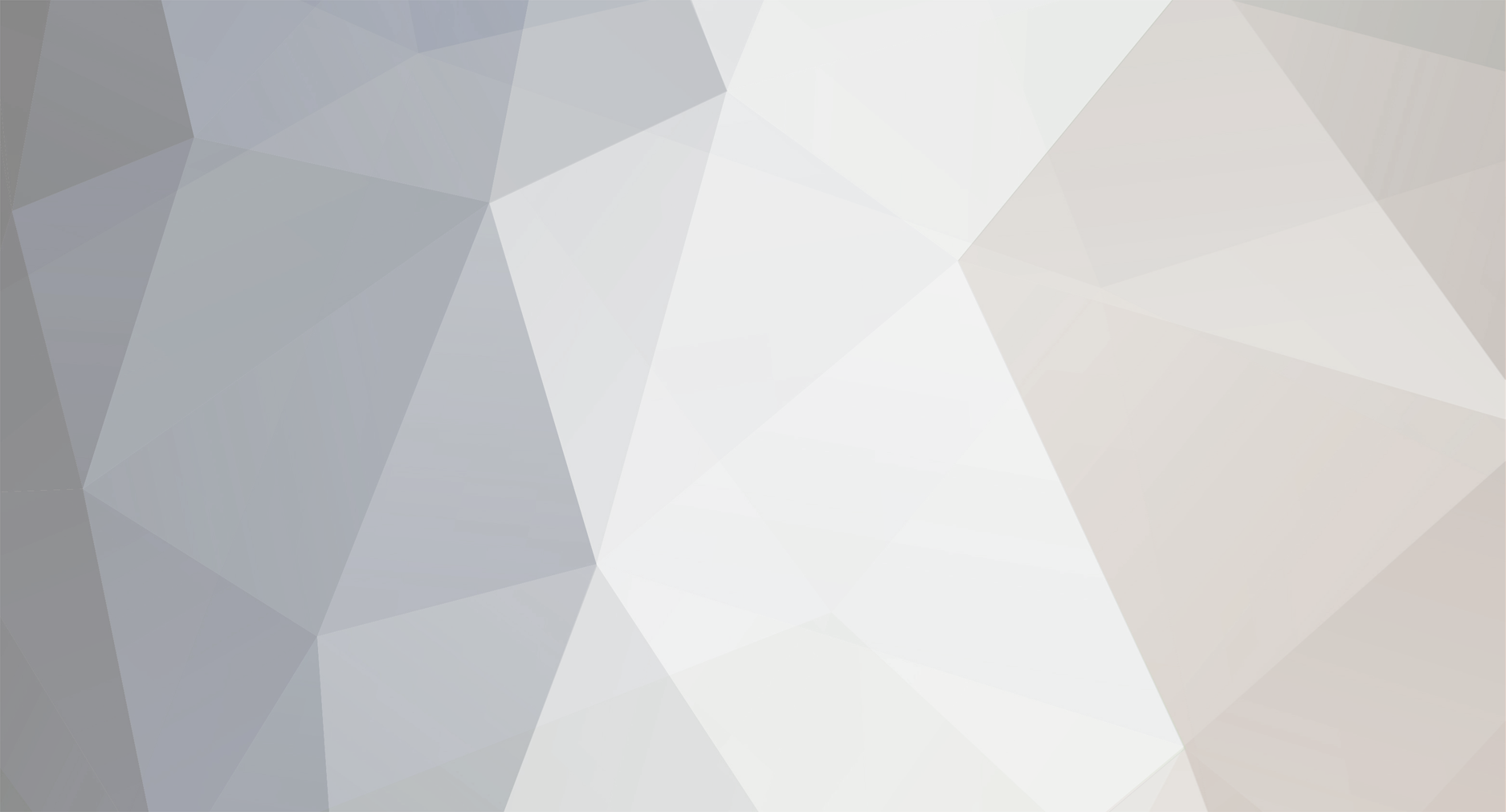
Landlubber Mike
-
Posts
1,221 -
Joined
-
Last visited
Content Type
Profiles
Forums
Events
Gallery
Posts posted by Landlubber Mike
-
-
Great work Rob - love the subtle weathering.
-
1
-
1
-
-
Taking a break from putting the finishing touches on the interior, I decided to spend some time on the engine. The kit engine is quite nice, but I picked up an engine that Vector makes specifically for this kit (VDS 48-118). Very detailed kit as you can see below.
Note: the Vector set includes a replacement bottom part for the engine housing. If you are building this kit with the Vector engine in the order in the instructions, you might miss this as the engine housing is built first on page 10, and the engine isn't built until page 15 of the instructions. This part is important as the Vector engine has a different shape to the underside than the kit part which is a little simplified. As part of the Vector set, you also have to trim off part of the pair of pipes that come down off the part containing the front pairs of legs.
My one pet peeve about this and other resin engines I've built (Aires, CMK) is that the propeller rod does not fit the kit propeller (way too narrow). Why can't they make the rod to fit the propeller?? Now I have to figure out how to make everything fit. 🤬
The engine took a few evenings to put together as I didn't want to rush gluing the cylinders in and having them out of line. In case you are deciding whether to buy the Vector set, as you can see in the picture below, the kit engine (left, dry fitted) is quite nice, but the Vector engine (right) really takes things up a couple of notches. I need to do a little filling and cleaning up, but otherwise, I'm really pleased with how the engine came out.
Here is the engine mount, where you can barely make out the Vector bottom piece in the second picture. I dry fitted the back pair of legs at the moment, as I want to button up the fuselage and test fit the engine mount before finalizing the mount. There's also an opening in the mount that you can see in the second picture. The kit provides two different parts that one can include on the side of the mount. I just need to pick one of them, since I'm building a different Walrus than the three included in the kit.
Interestingly (to me at least), the Walrus Pegasus engine/mount was pointed with an offset of 3 degrees to the left. The kit is designed this way, so kudos to Airfix.
Thanks for looking in!
-
9
-
-
1 hour ago, npb748r said:
Oh wow, that looks fantastic! I'll paint mine the same way. Thanks for the pictures. Did you install the three IP panels after putting the fuselage halves together? I was thinking of doing it that way, rather than the kit approach of adding them to the fuselage halves and then putting the halves together.
1 hour ago, npb748r said:The engine and panels is much bigger than the fuselage by almost the width of the plastic of the panel in some places. I'm going to live with it and pretend it's not there !
I'm probably not completely following you, but I think the engine and cowl area is supposed to be wider than where the fuselage halves end - in part, because I believe the aft part of the cowl is supposed to fit over the end of the fuselage halves rounded end, and line up close to what looks like the dotted lines along the halves. I think that the fuselage of the Buffalo generally stayed fairly consistent over time across the later variants, except to lengthen/widen the cowl and nose as the engines got bigger (looks like the B-239 reoriented the exhausts downward from along the sides of the cowl).
Here are some pictures from Naval Fighters Number 104. You can see the cowl is wider by about what you are describing, but maybe your kit is even wider than expected. First is of the F2A-3, the second two are of my variant, the B-239. Let me know if you are building a different variant and would like to see pictures. You can see that the bulge with the F2A-3 is considerably wider than the B-239, which is probably to be expected as the F2A-3 had a Wright 1820-40 Cylone of 1100HP, while the B-239 had a Wright 1820-G5 Cyclone of 950HP.
-
3
-
-
Thanks for passing that along Neil. Now that you mention it, I remember having an odd fit issue with the tail on my 1/48 build. I think I ended up sanding the main fuselage halves and then using filler here and there to make the transition to the tail seamless. I had done exactly what you did and put the tail halves together first, then tried adding it to the fuselage. I was pretty miffed, and I just tried to do the best I could with what I had. Thankfully, it's not a very obvious or eye drawing part section of the plane.
One question for you if you don't mind - to do the cockpit instrument panels using that film part and then the PE on top, did you first paint the plastic background piece white or silver before putting the film on top? I had painted the background black, but when i test fit the film on top it seemed way too dark and you couldn't see the dials.
-
2
-
-
Wow, that is really nice Hubert thanks for posting the pictures. Unfortunately the ignition harness is the wrong style (horseshoe versus circular for my engine) or I would have went for that one. I ended up ordering the PrintScale engine which I should hopefully receive soon.
Speaking of Vector, I have spent the last two nights putting together a Vector Pegasus engine for my Walrus. Must be nice to just take the engine out of the box and you're ready to go!
-
1
-
-
Beautiful work Peter, wow! Glad you got the decals to behave. Looks really fantastic, great job!
-
1
-
-
That Frank Drebin line always cracks me up!
-
3
-
2
-
-
Looks really sharp John! Well done!!
-
2
-
-
Thanks Peter! I was going to build just the plane and not include it in a diorama, but after coming across that picture, I don't think I can pass up the opportunity. It tells a cool story, and has just enough details in the picture to make it interesting - at least to me!
I'm itching to start working on it, but I really need to make some progress on the Walrus and Albatross to make the GB deadline. This time of year for me is usually pretty busy and modelling time is sparse 😬
-
1
-
-
Agree with Rob - at a minimum, go for upgraded brass barrels. If your kit doesn't come with PE railings, I'd get some of those as well. If it were me, I'd probably also look into adding pre-cut wooden decks and maybe some additional PE aftermarket like I used in my Shimakaze build (linked in my signature) or you see on Rob's current build.
PE (and now resin) aftermarket sets make a huge difference (and is almost a must for 1/700 in my opinion), but it all depends on what you want to get out of your build. The PE set for my Shimakaze build added at least double, and probably triple, the build time when you factor in adding all the details to guns, torpedo launchers, deck items, platforms, the bridge, etc. You can get comprehensive sets that have almost all of the upgraded detail you need, or you can add aftermarket a la carte as you need it. But, ship PE takes a certain level of discipline/masochism
-
5
-
-
2 hours ago, BlrwestSiR said:
Mike, I'm hoping it's all I need. Oddly enough, there's been a bunch of AM released recently for the kit. Aerocraft does a resin canopy and brass gear and Reskit is doing burner cans.
You can never have too much aftermarket...just saying!
-
2
-
1
-
-
Nice! Looking forward to seeing this one come alive. You probably went a little too light on the aftermarket though 😉
-
3
-
3
-
-
Looking really great Rob. Your work with the PE is pristine and it shows.
On Eduard's new decals, I heard of people having issues with them. Not exactly sure if people figured out a foolproof way to remove the carrier film.
-
2
-
1
-
-
2 hours ago, Martinnfb said:
Hi Mike, what a great choice of marking and super fast progress.., Regarding the wings, nothing is needed just proper preparation, I sanded the mating surface flat and glue them to the fuselage half beforehand. really , no drama there. Now, I am trying to figure out how to secure the undercarriage
Thanks Martin! Good to know on the wings. For the undercarriage, I believe I used CA - glued the pieces in, let it set, then flooded the non-visible area with more CA for added strength. The attachment points are a bit weak, at least they were on the 1/48 kit. Come to think of it, I might have also used some epoxy for the LG, but can't recall.
-
3
-
-
Oh I saw that one - looks like a sweet kit!
-
5
-
-
1 hour ago, Clunkmeister said:
Some people are leaders
Some are followers
Some need pictures drawn with Crayola to
Can you tell my wife that? 🤔
-
5
-
-
Thanks Ernie - as if there should be any debate!
-
4
-
-
21 hours ago, npb748r said:
Hi Mike, I thought of doing similar but because of that window in the belly of the plane anything that goes into the fuselage will be seen. I'm still scratching my head how best to approach this minor problem, interweb searching is underway as others must have dealt with this, we can't be the first builders of this kit. I'm guessing that the cockpit floor in the real plane is the main wing spar, otherwise I have no idea how the wings stayed on the aircraft ! Regarding the underwing lights, my instructions show both remain in place, I'm also off to hunt down some photos of RAF buffalo's. I've just glued the fuselage together, starting at the front and worked backwards. Not the prettiest of joins and filler required but most of the bigger gap is now at the back and underneath of the plane. It's almost as if the fuselage halves are banana shaped but your trick of installing the sub-components on one side first worked a treat - thank you.
neil
Neil, just remembered that our resident experts @Clunkmeister and @Martinnfb are building our kits. Ernie and Martin, did you guys do anything special to attach the wings on your Buffalos? Neil and I are getting close to that stage on our builds and are a bit disappointed in the kits' lack of anchor points for the wings.
-
3
-
-
On 3/11/2023 at 2:48 PM, CANicoll said:
And no more arguments about leaving the toilet seat up or down, or which side the TP unrolls from. Bonus!!
Chris
There is only one logical way to hang the TP roll!
-
4
-
-
41 minutes ago, HubertB said:
FYI, the Vector R-1820 is one that threw me into fits: because they did not understand the shape of the oil sump between the two lower cylinders (which, to simplify, looks like a fat « T » with rounded corners when viewed from above, with the vertical bar of the « T » between the two said cylinders), and to make space for it, they decided to widen the space between these two cylinders. Thus the 9 cylinders are not evenly distributed, with a 40° angle between each
…
I found a FPW model 1/32 R-1820 recently :
https://www.ebay.fr/itm/285150116289
Mine is on its way home from Poland, but it really looks promising, and much better than the wobbly Vector offering …
Hubert
PS: whilst the uneven polar distribution of the cylinders may not be an issue in the Buffalo cowling - although for me « once seen, never unseen » - it is one when you try to fit it into a cowling of the Grumman Gulfhawk with its bossings above the cylinder heads …
Thanks Hubert, that's very helpful to know. Maybe I'll skip the Vector and look elsewhere then. When looking for alternative R-1820s, I found the one you ordered:
Also found this one from PrintScale which looks promising:
The PrintScale one looks closer to the R-1820-G5 that my B-239 had (round ignition ring versus the more horseshoe-shaped one), though it looks like they have the ignition wiring opposite - the wire on the left side of the cylinder is wired into the front of the cylinder according to the picture below (from Naval Fighters Number 104), while PrintScale has the wire coming from the right side.
Ugh, never easy is it? Maybe I'll take a look at the Vector one and see what is going on with it.
-
5
-
1
-
-
After some noodling, I think I'm going to try to recreate this picture in a model diorama:
Sorry for using this log to record my thoughts, but I think I've worked through some of the trickier parts, which are:
1. Representing the BW-378 - fortunately, the kit includes decals for BW-378 (Camo C). The picture above suggests that the plane was re-painted/painted over in a winter camo scheme that looks very similar to the kit's scheme in Camo A, so I'll use A as the model with C's markings. Super lucky here, as not having the numbers would have probably made me scrap this whole crazy idea. The one thing I'm not sure about is whether in adding white for winter camo, the tail would have been repainted from white to blue - my guess is not since it seems like typical practice was to apply white paint over existing paint - here the olive and black areas of the plane - rather than repaint sections like the tail. Too bad though, as I think the blue tail looks pretty sharp.
2. Engine - with the panels open, I'll need to have a more detailed engine than the kit engine. The B-239 used a 950HP Wright R-1820-G5 Cyclone. Looking around, there are a few mid-late R-1820 aftermarket engines out there. Fortunately I already have a Vector engine (32-005) that looks like it might fit the bill. I had bought it for the Dauntless kit I won in the Christmas raffle here on LSM a few years ago, so I might try and use that one and see if it fits.
3. Cowl interior parts - on my 1/48 kit, I had opened similar panels using a CMK engine set which included the engine mounting pieces. For this 1/32 kit, it looks like things will be much simpler. I won't have to cut the access panels from the fuselage halves (as in step 1 on the 1/48 build) because the halves end in the right place since the 1/32 kit includes separate parts for the access panels. Plus, I believe that the 'curved-in' shape of the ends of the fuselage halves, together with the engine mounting pieces in the kit, get you PUR9 and PP1 and PP2 from the 1/48 kit (see instructions below). So, I think that all I will need to do is modify the kits access panels to show the one on the ground and the one held by the mechanic on top of the nose of the plane (which incudes the air vent, which should be fairly easy to replicate). Lucked out here (I hope) as replicating PUR9 wouldn't be easy.
4. Figures. Ultimately, these might be the trickiest parts of the diorama. I'll probably find figures that most closely match the poses of the three in the picture, and Frankenstein them with other parts like "winter heads with hats", gloves, and boots, and probably add or modify details using Milliput or similar materials.
5. Other diorama items. The ladder and wheel chocks should be fairly easy to replicate. The tarps will be tricky - I might use something like Modelspan, which I think I would be able to wet, fold and drape. If anyone has any other suggestions, I'd love to hear them. There are a few products to replicate snow, so hopefully that won't be an issue. I'd really like to replicate that birch tree in the background if I can - it adds a nice touch to the scene!
All in all, I think this might be a lot easier to accomplish than I first feared. Thanks for bearing with me on my little build treatise!
-
4
-
-
Wow PW!! Beautiful work!
-
3
-
-
2 hours ago, npb748r said:
I thought mine looked ok visually but just offered up the rear canopy and you are right, the right fuselage doesn't match the canopy . It's not out by much but it's really noticeable. I'm thinking I might try and reduce the canopy framework at the bottom to bring it down to the fuselage rather than build up the fuselage. Will be interesting to see if you have the same issue. I'm still working my way along the banana halves gluing the seam's where they popped undone as I remove the tap. Whilst extra work, it's not too hard to sort out and it's all part of the modelling experience. I will go for a shake and bake build after this one though (I need a simple 70's hasegawa kit but have none in my stash so will go searching for a cheap purchase !). Looking forward to your next steps !
neil
Well that sucks - was hoping that the rear canopy issue was only on the 1/48 kits. It wasn't quite as noticeable to me on the last kit until I started looking at fitting the canopy. Sorry also about the fuselage halves. The back half seems to fit fairly well, so what I might do is start by gluing the back half and maybe the bottom on the front halves, then work out what to do on the top of the front half. I'm worried that if I try to force the top half, I might have seams popping elsewhere as it looks like I could have a 2-3mm gap. Might be a better idea for me to close the gap with a piece of styrene.
I might put this one to the side for a bit, as I think I might attempt to do a diorama recreating one of the pictures I posted earlier (see my next post below), and I really need to get moving on my Walrus/Albatross group build project. So, you might end up passing me pretty quickly. I'm always happy to take a look at things if you have any questions and want to bounce things off someone.
-
3
-
-
Thanks Rob - I think that will show a bit more interesting details if I go that way, rather than show it as fully buttoned up and ready to launch off the catapult (kinda boring).
-
3
-
Soo.... What did you just get???
in Modelling Discussion
Posted
Rob, nice score! Interestingly, this was one of the first two plastic kits I bought from a fellow modeler on MSW to get back into the hobby. I really love the subject, but wanted to get my skills up before tackling it. It's a nice kit, but the Pontos set is insane - definitely try to find it as the added detail from that set is amazing.
Very cool that you built the Matchbox 1/72 kit. I also have the 1/72 Revell kit on the shelf with all the Great Little Ships upgrades. Now that I'm definitely waiting to improve my skills for that as the GLS stuff is pretty amazing, though I think learning to solder the bigger, heavier pieces of PE is a must.